funktionsfähige Futtermittel-Verladungsanlage "Dobuger"
Verfasst: 24. Oktober 2015, 07:47
Ich grüße euch,
in diesem Thread möchte ich euch meine neuste Kreation vorstellen: Eine funktionsfähige Rübenverladungsanlage. Die Idee kam mir auf dem Fremo H0e Treffen in Elfershausen. Dort hatte Dieter seine Rübenentladungsanlage in Form eines Miniaturstaubsaugers dabei. Mir war klar, dass es dann eigentlich auch eine Beladungsanlage benötigt. So war die Grundidee geboren.

Rübenentladungsanlage von Dieter beim Fremo H0e Treffen in Elfershausen
Ursprünglich hatte ich überlegt die Rüben mit einem Bagger zu beladen (es gibt ja von Roco eine funktionsfähige Baggerschaufel), aber mir erschien dieses Prozedere von der Beladung her zu zeitaufwändig. Daher bin ich umgeschwenkt: Eine große Siloanlage fasst die Rüben. Über ein Rohr werden die Rüben in die offenen Wagen entladen. Dabei wird von vornherein die Rollwagentauglichkeit berücksichtigt, um auch längere Umläufe inkl. Rollwagenverladung mit Normalspurwagen realisieren zu können.
Auf der Suche nach Ideen dazu bin ich beim Fremo Treffen in Rodgau von 2013 hängen geblieben. Dort gab es eine Getreideanlage, aber eben funktionslos. Mir ging es aber nur darum, einen Gleisplan zu finden und wie die Gebäude auf dem Gelände verteilt werden.

Getreideverladeanlage beim Fremo H0 Treffen in Rodgau

Getreideverladeanlage beim Fremo H0 Treffen in Rodgau

Getreideverladeanlage beim Fremo H0 Treffen in Rodgau
Daraufhin habe ich einen auf den Anschluss angepassten Gleisplan sowie passende Modulkästen gezeichnet. Der Bauplan kann wie immer als pdf gesichtet werden. Hier eine Version mit Maßangaben, hier eine Version ohne Maßangaben. Die Anbindung der Ladestelle erfolgt einseitig über eine Weichenverbindung. Die Schutzweiche dient gleichzeitig in ihrer Verlängerung als Abstellgleis. Nachträglich habe ich noch den linken Gleiswechsler eingebaut. Somit kann über das Umfahrgleis der Zug umfahren werden. Natürlich kann auch dieses Gleis als Abstellgleis dienen.
Wie es landschaftlich später ausschauen soll habe ich hier zusammen gefasst:

Die Grundkonstruktion besteht aus einfachen Modulkästen, die jedoch von den Maßen komplett identisch aufgebaut sind (abgesehen von den abgeschrägten Seiten zum 300 mm Übergang, das ist aber nicht von Bedeutung). Somit kann ich später bequem Türmchen stapeln. Es ergibt sich insgesamt ein Winkel von 12° auf einer Länge von etwas mehr als 2,6 m. Wie auch bei Mayrhofen habe ich von vornherein Passbuchsen eingebaut. An Gebäuden wird neben der Siloanlage von Walthers noch ein Siloturm von Faller (aus 130465) sowie Schuppen, Unterstände und eine LKW Waage zum Einsatz kommen.
Wie man sieht stehen die Silos schon da, denn die Verladeanlage muss natürlich als erstes gebaut werden.

Auch ein paar Gleise liegen schon aus. Wichtig waren v.a. die Weller Weichen, die mir Andreas wieder freundlicherweise in Rekordzeit zusammen gebaut hat. Nochmal vielen Dank dafür Andreas.

Hier sieht man grob aufgezeichnet, wo etwas später stehen soll.
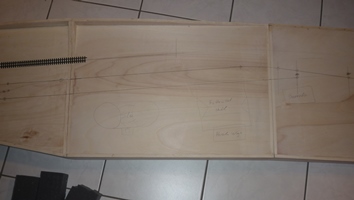
Bis ich die passenden Silos gefunden hatte, hat es doch etwas gedauert. Ursprünglich wollte ich den Futtermittel Handel Faller 130465 verwenden, aber die Silos hatten ja eine Höhe wie für Spur N und nicht H0. Es musste was größeres her. Dann bin ich doch auf die amerikanische Firma Walthers gestoßen und da gab es dann in der Tat passende Silos. Man muss zwar etwas tiefer in die Tasche greifen als bei Faller, aber das Ergebnis überzeugt. Die Silos werden, wenn alles so gebaut wird wie geplant, zusammen ein Fassungsvermögen von 4 l aufweisen. Damit lassen sich im Modell knapp 40 Eaos beladen. Also mehr als genug.

Und hier sieht man die Silos zusammen gebaut:

Das eigentlich komplexe an der ganzen Geschichte ist natürlich die funktionsfähige Rübenbeladung. Denn eine funktionslose Betriebsstelle wäre ja nur halb so spannend. Die Hauptfrage ist natürlich erstmal: Aus was besteht das Ladegut? Es ist Rotkleesaatgut. Das schaut in etwa aus wie Rüben und hat auch eine gute Körnergröße inkl. guter Rieselfähigkeit. Beim Fremo wird ebenfalls damit gearbeitet, daher macht es Sinn sich auf ein Ladegut festzulegen. So kann nicht nur das Ladegut freizügig unter den Betriebsstellen verteilt werden, es kann auch jeder auf den Zug aufspringen und ebenfalls eine Ladestelle auf Basis von Rotkleesaatgut bauen.

Das Grundprinzip zum befüllen ist dann recht schnell geboren: Über einen Trichter werden die Körner in ein Rohrsystem geleitet. Über zwei Winkel (ich schätze mit Winkel um die 65°) erreicht das Rohrsystem die Gleisachse und kann dort die Körner entladen. Ein wichtiges Kriterium ist natürlich noch der Rohrdurchmesser. Durch den Winkel darf dieser nicht zu klein sein, sonst verstopft das Rohr. Ich musste daher bis 12 mm Außen-, 10 mm Innendurchmesser gehen. Das ist natürlich in gewisser Weise eine unrealistisch große Rohrgröße, lässt sich aber nicht vermeiden. Trotzdem denke ich, dass es noch einigermaßen tolerierbar ist.
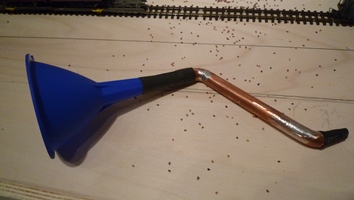
Dieses Rohr-Trichter-System habe ich mal vergleichsweise neben die Silos gestellt, damit man die Dimensionen erkennt. Das ganze wird also recht hoch. Damit das Getreide, das sich in den Silos befindet, irgendwie nach oben gelangt und dann in den Trichter rieseln kann - dazu habe ich mir auch schon was überlegt. Die Idee ist aber bisher nur in meinem Hirn vorhanden. Material dazu habe ich noch keines. Nach erfolgreichen Tests werde ich diese Idee dann ebenso vorstellen. Das Rohr mit dem Trichter wird sich später übrigens genau in der Mitte des Silos befinden, also an der verjüngten Stelle zwischen den beiden "Ofen"-Röhren.

So schaut dann ein fertig beladener Wagen aus.

Und wie er beladen wird sieht man hier (die Körner fülle ich natürlich aus einem Behälter in den Trichter, an der Grundfunktion wird sich später aber nichts ändern).
Link zum Video
Das Rohr wird später noch höhenverstellbar sein, damit es knapp über dem Wagen abgesenkt werden kann. Wenn die Körner aus zu großer Höhe fallen, springen sie auf dem Wagenboden auf und fallen wieder heraus. Außerdem soll das Rohr auch drehbar gelagert werden, damit ein Wagen (zumindest bis zu einer bestimmten Länge) auch ohne einer Zugbewegung beladen werden kann. Grundsätzlich muss aber nach jeder Wagenladung der Zug um ein Stück weiter geschoben werden, damit der nächste Wagen beladen werden kann.
Es kam Material: Viele Tillig Gleise...

... und schon Ausgestaltungsmaterial: Faller 130465 Futtermittel-Handel, wobei ich nur den rechteckigen Bau benötige. Die runden Silos verkaufe ich wieder, dazu habe ich ja die Walthers Silo. Die Faller Silos sind mir zu niedrig. Dazu noch Busch 1544 Baracke und Busch 1456 Fahrzeughalle

Der Gleisbau ist abgeschlossen, wobei die Weichen noch nicht mit Antrieben versehen sind und die Anschlusskabel für die Gleise nur lose herunter hängen. Wie man es von mir gewohnt ist, habe ich wieder auf eine sehr ordentlichen Gleisverlegung geachtet, damit es zu keinen Entgleisungen kommt.

Die Walthers Silos und der rechteckige Siloturm von Faller (aus 130465) sind platziert.

Ich habe das Dach mal noch nicht festgeklebt, da man den Hohlraum doch eigentlich nutzen kann. Entweder Futtermittel Nachschub oder Getränkehalter?

Die Busch 1544 Baracke ist zusammengebaut.

Sie ist aber doch irgendwie recht klein geraten. Ich hatte nicht wirklich auf die Abmessungen geachtet und kann mir das meistens ohnehin nie richtig vorstellen. Aber ich bin am überlegen, ob ich mir da lieber nicht was größeres hole?
Und die Busch 1456 Fahrzeughalle ist auch montiert. Die passt von der Größe aber perfekt. An dem nicht ganz angeklebten Dachabschluss bitte nicht stören. Ich habe das komplette Dach noch nicht festgeklebt, damit ich es abnehmen kann, um das Innenleben zu gestalten und zu beleuchten. Außerdem kann davon ausgegangen werden, dass sich einige Türchen mechanisch bzw. elektrisch öffnen werden...


Die Futtermittel-Verladeanlage funktioniert mittlerweile wie ich es mir vorgestellt habe. Lange habe ich überlegt, wie ich das Schüttgut in den Trichter befördern soll. Schließlich soll in den Silos viel Schüttgut gelagert werden, damit nicht ständig nachgefüllt werden muss. Dazu muss aber irgendwie das Schüttgut nach oben gepumpt werden, denn die Oberkante des Trichters liegt fast an der Dachkante des Silos. Mir kam dann eine Idee: In den beiden Silos befindet sich je ein Zylinder. Über einen Kolben wird das Schüttgut nach oben gedrückt und fällt dann über eine Auslage in den Trichter.
Das ist natürlich nur gedacht. Jetzt muss die Idee auch umgesetzt werden. Für die Zylinder werden unterhalb der Silos in die Anlagenplatte zwei große Löcher gesägt.

Der Trichter wird sowohl höhen- als auch seitenverstellbar gelagert. Dies hat zwei Gründe: Die Höhenverstellung ist notwendig, damit sowohl niedrige H0e als auch augeschemelte H0 Wagen beladen werden können. Eine Fixierung in oberer Position ist jedoch für niedrige Wagen nicht praktikabel, da das herunterfallende Schüttgut auf den Wagenboden aufprallt und sofort aus dem Wagen springt. Es wäre somit das gesamte Umfeld beladen, nicht aber der Wagen selber. Die Drehbarkeit habe ich als zweckmäßig erachtet, da es somit möglich ist, einen länglichen Bereich zu beladen, ohne den Zug jedesmal zu bewegen.
Damit der Trichter überhaupt Platz hat muss innerhalb der Silos Material weg gefräst werden.

Über Kunststoffplatten wird eine glatte Fläche geschaffen, damit der Trichter nicht an den Silokanten hängen bleibt.


Nun kommen die zwei großen Röhren zum Einsatz.

Passgenau wird ein Holzkreis ausgesägt. Darauf wird eine Gummidichtung geklebt. Die Dichtung sorgt für eine bessere Haftung des Silikons…

… denn der Spalt zwischen Dichtung und Rohr muss mit Silikon ausgefüllt werden, damit kein Schüttgut auf den Boden rieselt.

Das Rohr wird vorher in einem kleinen Bereich mit Gleitmittel
eingestrichen, damit das Silikon dort nicht haftet und sich am Rohr festklebt.

So schaut die Anlage nun schon mal aus. Der Bereich zwischen den beiden Silos wird noch mit einem Teil verkleidet, dort muss vorher aber ein Schlitz für den Schüttarm gefräst werden.

Auf der Rückseite sieht man schon mal, wie die Verkleidung später die Technik kaschiert.


Futtermittel-Haus und Siloanlage:

Der Silokomplex kann nun auf die Grundplatte geschraubt werden. Mir erschien nur kleben als nicht dauerhaft stabil genug. Zu groß wäre mir die Gefahr gewesen, dass beim Transport der Silo abfällt und beschädigt wird. Daher habe ich Gewindemuttern in den Silo eingeklebt und von unten mit Gewindeschrauben fest geschraubt.


Für das Bedienpult habe ich eine Aussparung gebaut. Hier werden zwei Stellstäbe für die Höhen- und Seitenverstellung, ein Taster zum Einschalten sowie Leuchtmelder die den Füllstand anzeigen eingebaut.

Für die Umsetzung Mechanik der Höhen- und Seitenverstellung des Ausfüllarms musste ich ein wenig überlegen. Es war gar nicht so einfach. Die Ausführung nur eine der beiden Bewegungen ist sicherlich keine Schwierigkeit, aber beides unabhängig voneinander? Wird der Arm in der Höhe verstellt, wandert auch der Angriffspunkt für die Seitenverstellung mit und verändert dadurch den Abstand zur Stellstange.
Mir kam dann die Idee an den Stab für den Ausfüllarm eine Art Ruder anzubauen. Dieses wird von einem quer dazu verlaufenden mit einer Kerbe versehenen Profil in Position gehalten. Wird der Ausfüllarm in der Höhe verstellt, so bleibt das Ruder trotzdem in Position und gleitet durch die Kerbe.
Hier sieht man schon mal die beiden Stellstangen, sowie das mit einem Ruder versehenen Rohr des Ausfüllarms.

Fertig schaut die Konstruktion schließlich wie folgt aus:

Das Profil für die Drehbewegung:

Wie man sieht bleibt das Ruder bei jeder Höhe in Position. Drehen und Höhenverstellung erfolgt somit unabhängig voneinander.


Übrigens benötigt man zum Verlöten von solchen Messingmassen schon ein wenig mehr Hitze. Ich habe daher öfters zur Heißluftpistole gegriffen. Daher sieht man teilweise auch ein wenig „Röstspuren“ am Holz, was jedoch keine weiteren Nachwirkungen hat.

Die Stellstange für die Höhenverstellung erhält noch ein Gegengewicht, damit der schwere Arm ohne großen Kraftaufwand bewegt werden kann. Es bleibt lediglich eine geringe Haftkraft zurück, die den Arm in Position hält. Das Gegengewicht besteht übrigens aus Bleikugeln, die in Leim eingelassen sind. Das Gewicht wird später noch etwas angemalt, damit es nicht ganz so abstrus ausschaut.

Als nächstes habe ich mir Gedanken zum Bewegen des Kolbens gemacht. Hierbei habe ich mir ein im Modellbau oft angewendetes Prinzip zu Nutze gemacht: Eine Gewindemutter dreht sich um eine Gewindestange und treibt diese entweder nach oben oder nach unten. Dazu wird am Kolben eben eine solche Gewindestange befestigt. Dies geschieht über drei ins Holz gedrehte Schrauben, die mit der Gewindestange verlötet werden.


Wie man sieht habe ich noch eine Führung eingebaut. Diese sorgt dafür, dass sich der Kolben nicht mit dreht, sondern in Position bleibt. Andernfalls würde es natürlich nicht zu einer Hubbewegung kommen. In der Führung befinden sich noch zwei Kabel, die an einen Endschalter angeschlossen werden.

Außerdem ist der Ausfüllschacht eingebaut. Hierbei kommen zwei U-Profile zum Einsatz, die schräg miteinander verklebt werden. Am unteren Ende habe ich ein Loch gebohrt, in das ein Rohr gesteckt wird. Dieses befindet sich direkt über dem Trichter und sorgt dafür, dass das Schüttgut gezielt in den Trichter fällt.

Das Schüttgut wird durch den Kolben nach oben gedrückt und fällt schließlich in den Ausfüllschacht.

Als nächstes wird die Gewindemutter in ein Rohr gelötet. Später wird das Rohr angetrieben und dreht dadurch die Mutter. Damit die Mutter aber auch ins Rohr passt, muss sie rund geschliffen werden.


Zum Einlöten empfiehlt es sich eine Gewindestange einzuführen und zu zentrieren, damit die Gewindemutter auch waagrecht eingelötet wird und später nicht schrägt sitzt und das ganze System eiert.

Fertig.

Nun habe ich zwei große Rohre in einem mittelgroßen Abstand die ich irgendwie antreiben muss. Aber wie mache ich das am besten? Es war eigentlich die Kopfzerbrechendste Sache an der ganzen Geschichte. Zuerst überlegte ich die Rohre über einen Zahnriemen zu verbinden, der von einem Motor angetrieben wird. Und noch manch andere Gedanken hatte ich, die aber nicht zielführend waren. Dazu hat auch noch das Rohr solche Abmessungen, die natürlich in Kombination mit Ritzeln überhaupt nicht passen.
Irgendwann hatte ich dann aber doch einen Einfall. Mit nur hinreichend großen Zahnrädern sollten Fünf an der Zahl bereits ausreichen, um das Ganze zu motorisieren. Je ein Zahnrad für die beiden Rohre, ein Zahnrad für den Motor und zwei Zahnräder als Zwischenzahnrad zwischen Motor und Rohr. Also habe ich passende Zahnräder aus Vollmessing gekauft, dazu noch paar Kugellager und eine Welle. Diese Zahnräder liegen natürlich in einer anderen Preisliga als Kunststoffzahnräder in Miniaturgröße, aber ich denke dass durch die Größe eine gewisse Robustheit mit einhergeht und das System dadurch lange in Betrieb stehen kann.
Kompliziert war noch ein passendes Zahnrad für das Rohr zu finden. Mein erster Gedanke war ein Zahnrad zu suchen, dessen Bohrung dem Außendurchmesser des Rohrs entspricht. Diese Suche ist aber erfolglos verlaufen. Dann bin ich auf Zahnräder mit Nabe gestoßen. Auch hier hatte zwar kein Zahnrad eine Nabe, deren Außendurchmesser dem Innendurchmesser des Rohrs entsprach, aber es gab eine Nabe, die nur ein Millimeter kleiner im Durchmesser war. Die 0,5 mm Luftspalt zwischen Rohrinnenwand und Nabe habe ich mit einer 0,5 mm starken Kunststoffplatte ausgefüllt und das Ritzel unter Zuführung von Sekundenkleber in das Rohr gepresst.
Aber was nützt einem nun die schönste Getriebekonstruktion wenn man die Zahnräder nicht lagern kann? Solch eine Lagerung mit konventioneller Säge und Bohrer selber bauen ist eigentlich nicht möglich. Zum einen haben die Kugellager solch spezielle Abmessungen, dass es dafür wohl keinen Bohrer gibt. Dann erfordert es noch solch hohe Präzision, dass man eigentlich ohne Fräsen nicht auskommt. Wie gut also, wenn man da jemanden kennt, der eine schöne Fräse daheim stehen hat. Ich habe mit unserem Bruchflieger Daniel Kontakt aufgenommen und er hat mir eine Lagerung aus Holz gefräst. Vorab musste ich dazu AutoCAD anwerfen und eine Zeichnung erstellen. Daniel hatte noch gute Ideen und baute gleich Abstandshalter ein, so dass der Getriebekasten am Ende nicht nur funktional und höchst präzise, sondern wie ich finde auch in einer gewissen Schönheit bei mir ankam. An dieser Stelle nochmal vielen Dank an Daniel für seine super gute Unterstützung und die schnelle Umsetzung.
Auf der unteren Platte werden die beiden Zwischenzahnräder eingesetzt. Das mittlere Kugellager ist für die Motorwelle.

Auf der oberen Platte folgen die beiden Rohre.

Dann kann beides verheiratet werden. In die Aussparung kommt der Getriebemotor hinein.


Ich habe mich hierzu für einen Getriebemotor von Conrad entschieden.

Das Zahnrad auf der Motorwelle fest zu montieren war gar nicht so einfach, aber ich habe es mit etwas Lötzinn dann geschafft.

Der Motor wird über einen Winkel und ein Holzbrett mit zwei Gewindeschrauben befestigt.


Fertig schaut die abenteuerliche Mechanik so aus:

Auch oben befindet sich eine Lagerung der beiden Rohre.

Hier sieht man einen beladenen und einen nicht beladenen Silo zu Testzwecken.

Und hier ein Video welches zeigt, dass alles funktioniert.
Leider dreht der Getriebemotor doch zu schnell, so dass bei normaler Betriebsspannung zu viel Schüttgut auf einmal in den Wagen fällt. Der Wagen belädt sich dann zu schnell, so dass es leicht passieren kann, dass er überfüllt wird. Hier muss ich also nochmal einen anderen Motor mit niedrigerer Umdrehungszahl kaufen.
Was derzeit noch ein kleines Problem ist, ist der „Nachlauf“ des Schüttguts. Bereits bei leichten Vibrationen fällt Schüttgut nach. Wenn kein Wagen auf dem Gleis steht, wird also im Laufe der Betriebstage das Gleis „befüllt“. Hier muss ich wohl noch etwas grübeln. Da ich aber ohnehin eine Steuerung für die Leuchtmelder zur Anzeige des Füllstands einbauen möchte, kann ich auch eine Automatik programmieren, die den Kolben bei längerer Nichtbenutzung wieder ein wenig nach unten fährt.
Nebenbei geht es auch an der Ausgestaltung weiter. Das Hauptgebäude neben den Silos wird wie der Silo auch mit Schrauben auf der Anlagenplatte befestigt. Hierzu wurden L-Profile an die Unterseite des Gebäudes geklebt. Die L-Profile haben mehr Verbindungsfläche zum Gebäude als die dünne Gebäudewand zum Boden.

Auf der Anlagenplatte werden Unterlegstücke eingebaut, welche den Höhenunterschied des Kopfsteinpflasters überbrücken. Außerdem noch ein Rohr. Wou denn das?

Von unten kommt ein Boden hinzu.


Von außen unscheinbar…

… Dach ab. Ich konnte es mir nicht verkneifen
Und ich denke der Platz ist sinnvoll genutzt. So einfach verschenken konnte ich den Freiraum nun doch nicht.

Im Landschaftsbau geht es auf dem ersten Segment schon gut voran. Die Anhöhe am Seitenrand wird mit Styrodor und etwas Gips gestaltet.
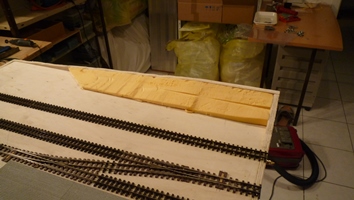
Mittlerweile ist dieses Segment bereits komplett geerdet und geschottert.

Als Gleisabschluss habe ich mich diesmal für Veit Prellböcke entschieden.

Und so schaut der Komplex aktuell aus.

Gruß
Dominik
in diesem Thread möchte ich euch meine neuste Kreation vorstellen: Eine funktionsfähige Rübenverladungsanlage. Die Idee kam mir auf dem Fremo H0e Treffen in Elfershausen. Dort hatte Dieter seine Rübenentladungsanlage in Form eines Miniaturstaubsaugers dabei. Mir war klar, dass es dann eigentlich auch eine Beladungsanlage benötigt. So war die Grundidee geboren.

Rübenentladungsanlage von Dieter beim Fremo H0e Treffen in Elfershausen
Ursprünglich hatte ich überlegt die Rüben mit einem Bagger zu beladen (es gibt ja von Roco eine funktionsfähige Baggerschaufel), aber mir erschien dieses Prozedere von der Beladung her zu zeitaufwändig. Daher bin ich umgeschwenkt: Eine große Siloanlage fasst die Rüben. Über ein Rohr werden die Rüben in die offenen Wagen entladen. Dabei wird von vornherein die Rollwagentauglichkeit berücksichtigt, um auch längere Umläufe inkl. Rollwagenverladung mit Normalspurwagen realisieren zu können.
Auf der Suche nach Ideen dazu bin ich beim Fremo Treffen in Rodgau von 2013 hängen geblieben. Dort gab es eine Getreideanlage, aber eben funktionslos. Mir ging es aber nur darum, einen Gleisplan zu finden und wie die Gebäude auf dem Gelände verteilt werden.

Getreideverladeanlage beim Fremo H0 Treffen in Rodgau

Getreideverladeanlage beim Fremo H0 Treffen in Rodgau

Getreideverladeanlage beim Fremo H0 Treffen in Rodgau
Daraufhin habe ich einen auf den Anschluss angepassten Gleisplan sowie passende Modulkästen gezeichnet. Der Bauplan kann wie immer als pdf gesichtet werden. Hier eine Version mit Maßangaben, hier eine Version ohne Maßangaben. Die Anbindung der Ladestelle erfolgt einseitig über eine Weichenverbindung. Die Schutzweiche dient gleichzeitig in ihrer Verlängerung als Abstellgleis. Nachträglich habe ich noch den linken Gleiswechsler eingebaut. Somit kann über das Umfahrgleis der Zug umfahren werden. Natürlich kann auch dieses Gleis als Abstellgleis dienen.
Wie es landschaftlich später ausschauen soll habe ich hier zusammen gefasst:

Die Grundkonstruktion besteht aus einfachen Modulkästen, die jedoch von den Maßen komplett identisch aufgebaut sind (abgesehen von den abgeschrägten Seiten zum 300 mm Übergang, das ist aber nicht von Bedeutung). Somit kann ich später bequem Türmchen stapeln. Es ergibt sich insgesamt ein Winkel von 12° auf einer Länge von etwas mehr als 2,6 m. Wie auch bei Mayrhofen habe ich von vornherein Passbuchsen eingebaut. An Gebäuden wird neben der Siloanlage von Walthers noch ein Siloturm von Faller (aus 130465) sowie Schuppen, Unterstände und eine LKW Waage zum Einsatz kommen.
Wie man sieht stehen die Silos schon da, denn die Verladeanlage muss natürlich als erstes gebaut werden.

Auch ein paar Gleise liegen schon aus. Wichtig waren v.a. die Weller Weichen, die mir Andreas wieder freundlicherweise in Rekordzeit zusammen gebaut hat. Nochmal vielen Dank dafür Andreas.

Hier sieht man grob aufgezeichnet, wo etwas später stehen soll.
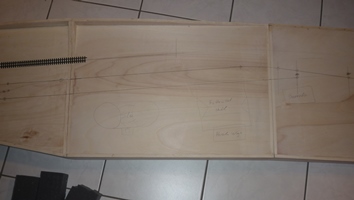
Bis ich die passenden Silos gefunden hatte, hat es doch etwas gedauert. Ursprünglich wollte ich den Futtermittel Handel Faller 130465 verwenden, aber die Silos hatten ja eine Höhe wie für Spur N und nicht H0. Es musste was größeres her. Dann bin ich doch auf die amerikanische Firma Walthers gestoßen und da gab es dann in der Tat passende Silos. Man muss zwar etwas tiefer in die Tasche greifen als bei Faller, aber das Ergebnis überzeugt. Die Silos werden, wenn alles so gebaut wird wie geplant, zusammen ein Fassungsvermögen von 4 l aufweisen. Damit lassen sich im Modell knapp 40 Eaos beladen. Also mehr als genug.

Und hier sieht man die Silos zusammen gebaut:

Das eigentlich komplexe an der ganzen Geschichte ist natürlich die funktionsfähige Rübenbeladung. Denn eine funktionslose Betriebsstelle wäre ja nur halb so spannend. Die Hauptfrage ist natürlich erstmal: Aus was besteht das Ladegut? Es ist Rotkleesaatgut. Das schaut in etwa aus wie Rüben und hat auch eine gute Körnergröße inkl. guter Rieselfähigkeit. Beim Fremo wird ebenfalls damit gearbeitet, daher macht es Sinn sich auf ein Ladegut festzulegen. So kann nicht nur das Ladegut freizügig unter den Betriebsstellen verteilt werden, es kann auch jeder auf den Zug aufspringen und ebenfalls eine Ladestelle auf Basis von Rotkleesaatgut bauen.

Das Grundprinzip zum befüllen ist dann recht schnell geboren: Über einen Trichter werden die Körner in ein Rohrsystem geleitet. Über zwei Winkel (ich schätze mit Winkel um die 65°) erreicht das Rohrsystem die Gleisachse und kann dort die Körner entladen. Ein wichtiges Kriterium ist natürlich noch der Rohrdurchmesser. Durch den Winkel darf dieser nicht zu klein sein, sonst verstopft das Rohr. Ich musste daher bis 12 mm Außen-, 10 mm Innendurchmesser gehen. Das ist natürlich in gewisser Weise eine unrealistisch große Rohrgröße, lässt sich aber nicht vermeiden. Trotzdem denke ich, dass es noch einigermaßen tolerierbar ist.
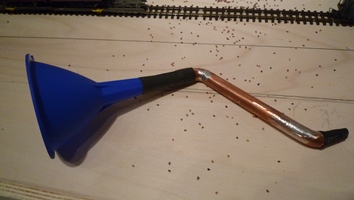
Dieses Rohr-Trichter-System habe ich mal vergleichsweise neben die Silos gestellt, damit man die Dimensionen erkennt. Das ganze wird also recht hoch. Damit das Getreide, das sich in den Silos befindet, irgendwie nach oben gelangt und dann in den Trichter rieseln kann - dazu habe ich mir auch schon was überlegt. Die Idee ist aber bisher nur in meinem Hirn vorhanden. Material dazu habe ich noch keines. Nach erfolgreichen Tests werde ich diese Idee dann ebenso vorstellen. Das Rohr mit dem Trichter wird sich später übrigens genau in der Mitte des Silos befinden, also an der verjüngten Stelle zwischen den beiden "Ofen"-Röhren.

So schaut dann ein fertig beladener Wagen aus.

Und wie er beladen wird sieht man hier (die Körner fülle ich natürlich aus einem Behälter in den Trichter, an der Grundfunktion wird sich später aber nichts ändern).
Link zum Video
Das Rohr wird später noch höhenverstellbar sein, damit es knapp über dem Wagen abgesenkt werden kann. Wenn die Körner aus zu großer Höhe fallen, springen sie auf dem Wagenboden auf und fallen wieder heraus. Außerdem soll das Rohr auch drehbar gelagert werden, damit ein Wagen (zumindest bis zu einer bestimmten Länge) auch ohne einer Zugbewegung beladen werden kann. Grundsätzlich muss aber nach jeder Wagenladung der Zug um ein Stück weiter geschoben werden, damit der nächste Wagen beladen werden kann.
Es kam Material: Viele Tillig Gleise...

... und schon Ausgestaltungsmaterial: Faller 130465 Futtermittel-Handel, wobei ich nur den rechteckigen Bau benötige. Die runden Silos verkaufe ich wieder, dazu habe ich ja die Walthers Silo. Die Faller Silos sind mir zu niedrig. Dazu noch Busch 1544 Baracke und Busch 1456 Fahrzeughalle

Der Gleisbau ist abgeschlossen, wobei die Weichen noch nicht mit Antrieben versehen sind und die Anschlusskabel für die Gleise nur lose herunter hängen. Wie man es von mir gewohnt ist, habe ich wieder auf eine sehr ordentlichen Gleisverlegung geachtet, damit es zu keinen Entgleisungen kommt.

Die Walthers Silos und der rechteckige Siloturm von Faller (aus 130465) sind platziert.

Ich habe das Dach mal noch nicht festgeklebt, da man den Hohlraum doch eigentlich nutzen kann. Entweder Futtermittel Nachschub oder Getränkehalter?

Die Busch 1544 Baracke ist zusammengebaut.

Sie ist aber doch irgendwie recht klein geraten. Ich hatte nicht wirklich auf die Abmessungen geachtet und kann mir das meistens ohnehin nie richtig vorstellen. Aber ich bin am überlegen, ob ich mir da lieber nicht was größeres hole?
Und die Busch 1456 Fahrzeughalle ist auch montiert. Die passt von der Größe aber perfekt. An dem nicht ganz angeklebten Dachabschluss bitte nicht stören. Ich habe das komplette Dach noch nicht festgeklebt, damit ich es abnehmen kann, um das Innenleben zu gestalten und zu beleuchten. Außerdem kann davon ausgegangen werden, dass sich einige Türchen mechanisch bzw. elektrisch öffnen werden...



Die Futtermittel-Verladeanlage funktioniert mittlerweile wie ich es mir vorgestellt habe. Lange habe ich überlegt, wie ich das Schüttgut in den Trichter befördern soll. Schließlich soll in den Silos viel Schüttgut gelagert werden, damit nicht ständig nachgefüllt werden muss. Dazu muss aber irgendwie das Schüttgut nach oben gepumpt werden, denn die Oberkante des Trichters liegt fast an der Dachkante des Silos. Mir kam dann eine Idee: In den beiden Silos befindet sich je ein Zylinder. Über einen Kolben wird das Schüttgut nach oben gedrückt und fällt dann über eine Auslage in den Trichter.
Das ist natürlich nur gedacht. Jetzt muss die Idee auch umgesetzt werden. Für die Zylinder werden unterhalb der Silos in die Anlagenplatte zwei große Löcher gesägt.

Der Trichter wird sowohl höhen- als auch seitenverstellbar gelagert. Dies hat zwei Gründe: Die Höhenverstellung ist notwendig, damit sowohl niedrige H0e als auch augeschemelte H0 Wagen beladen werden können. Eine Fixierung in oberer Position ist jedoch für niedrige Wagen nicht praktikabel, da das herunterfallende Schüttgut auf den Wagenboden aufprallt und sofort aus dem Wagen springt. Es wäre somit das gesamte Umfeld beladen, nicht aber der Wagen selber. Die Drehbarkeit habe ich als zweckmäßig erachtet, da es somit möglich ist, einen länglichen Bereich zu beladen, ohne den Zug jedesmal zu bewegen.
Damit der Trichter überhaupt Platz hat muss innerhalb der Silos Material weg gefräst werden.

Über Kunststoffplatten wird eine glatte Fläche geschaffen, damit der Trichter nicht an den Silokanten hängen bleibt.


Nun kommen die zwei großen Röhren zum Einsatz.

Passgenau wird ein Holzkreis ausgesägt. Darauf wird eine Gummidichtung geklebt. Die Dichtung sorgt für eine bessere Haftung des Silikons…

… denn der Spalt zwischen Dichtung und Rohr muss mit Silikon ausgefüllt werden, damit kein Schüttgut auf den Boden rieselt.

Das Rohr wird vorher in einem kleinen Bereich mit Gleitmittel


So schaut die Anlage nun schon mal aus. Der Bereich zwischen den beiden Silos wird noch mit einem Teil verkleidet, dort muss vorher aber ein Schlitz für den Schüttarm gefräst werden.

Auf der Rückseite sieht man schon mal, wie die Verkleidung später die Technik kaschiert.


Futtermittel-Haus und Siloanlage:

Der Silokomplex kann nun auf die Grundplatte geschraubt werden. Mir erschien nur kleben als nicht dauerhaft stabil genug. Zu groß wäre mir die Gefahr gewesen, dass beim Transport der Silo abfällt und beschädigt wird. Daher habe ich Gewindemuttern in den Silo eingeklebt und von unten mit Gewindeschrauben fest geschraubt.


Für das Bedienpult habe ich eine Aussparung gebaut. Hier werden zwei Stellstäbe für die Höhen- und Seitenverstellung, ein Taster zum Einschalten sowie Leuchtmelder die den Füllstand anzeigen eingebaut.

Für die Umsetzung Mechanik der Höhen- und Seitenverstellung des Ausfüllarms musste ich ein wenig überlegen. Es war gar nicht so einfach. Die Ausführung nur eine der beiden Bewegungen ist sicherlich keine Schwierigkeit, aber beides unabhängig voneinander? Wird der Arm in der Höhe verstellt, wandert auch der Angriffspunkt für die Seitenverstellung mit und verändert dadurch den Abstand zur Stellstange.
Mir kam dann die Idee an den Stab für den Ausfüllarm eine Art Ruder anzubauen. Dieses wird von einem quer dazu verlaufenden mit einer Kerbe versehenen Profil in Position gehalten. Wird der Ausfüllarm in der Höhe verstellt, so bleibt das Ruder trotzdem in Position und gleitet durch die Kerbe.
Hier sieht man schon mal die beiden Stellstangen, sowie das mit einem Ruder versehenen Rohr des Ausfüllarms.

Fertig schaut die Konstruktion schließlich wie folgt aus:

Das Profil für die Drehbewegung:

Wie man sieht bleibt das Ruder bei jeder Höhe in Position. Drehen und Höhenverstellung erfolgt somit unabhängig voneinander.


Übrigens benötigt man zum Verlöten von solchen Messingmassen schon ein wenig mehr Hitze. Ich habe daher öfters zur Heißluftpistole gegriffen. Daher sieht man teilweise auch ein wenig „Röstspuren“ am Holz, was jedoch keine weiteren Nachwirkungen hat.

Die Stellstange für die Höhenverstellung erhält noch ein Gegengewicht, damit der schwere Arm ohne großen Kraftaufwand bewegt werden kann. Es bleibt lediglich eine geringe Haftkraft zurück, die den Arm in Position hält. Das Gegengewicht besteht übrigens aus Bleikugeln, die in Leim eingelassen sind. Das Gewicht wird später noch etwas angemalt, damit es nicht ganz so abstrus ausschaut.

Als nächstes habe ich mir Gedanken zum Bewegen des Kolbens gemacht. Hierbei habe ich mir ein im Modellbau oft angewendetes Prinzip zu Nutze gemacht: Eine Gewindemutter dreht sich um eine Gewindestange und treibt diese entweder nach oben oder nach unten. Dazu wird am Kolben eben eine solche Gewindestange befestigt. Dies geschieht über drei ins Holz gedrehte Schrauben, die mit der Gewindestange verlötet werden.


Wie man sieht habe ich noch eine Führung eingebaut. Diese sorgt dafür, dass sich der Kolben nicht mit dreht, sondern in Position bleibt. Andernfalls würde es natürlich nicht zu einer Hubbewegung kommen. In der Führung befinden sich noch zwei Kabel, die an einen Endschalter angeschlossen werden.

Außerdem ist der Ausfüllschacht eingebaut. Hierbei kommen zwei U-Profile zum Einsatz, die schräg miteinander verklebt werden. Am unteren Ende habe ich ein Loch gebohrt, in das ein Rohr gesteckt wird. Dieses befindet sich direkt über dem Trichter und sorgt dafür, dass das Schüttgut gezielt in den Trichter fällt.

Das Schüttgut wird durch den Kolben nach oben gedrückt und fällt schließlich in den Ausfüllschacht.

Als nächstes wird die Gewindemutter in ein Rohr gelötet. Später wird das Rohr angetrieben und dreht dadurch die Mutter. Damit die Mutter aber auch ins Rohr passt, muss sie rund geschliffen werden.


Zum Einlöten empfiehlt es sich eine Gewindestange einzuführen und zu zentrieren, damit die Gewindemutter auch waagrecht eingelötet wird und später nicht schrägt sitzt und das ganze System eiert.

Fertig.

Nun habe ich zwei große Rohre in einem mittelgroßen Abstand die ich irgendwie antreiben muss. Aber wie mache ich das am besten? Es war eigentlich die Kopfzerbrechendste Sache an der ganzen Geschichte. Zuerst überlegte ich die Rohre über einen Zahnriemen zu verbinden, der von einem Motor angetrieben wird. Und noch manch andere Gedanken hatte ich, die aber nicht zielführend waren. Dazu hat auch noch das Rohr solche Abmessungen, die natürlich in Kombination mit Ritzeln überhaupt nicht passen.
Irgendwann hatte ich dann aber doch einen Einfall. Mit nur hinreichend großen Zahnrädern sollten Fünf an der Zahl bereits ausreichen, um das Ganze zu motorisieren. Je ein Zahnrad für die beiden Rohre, ein Zahnrad für den Motor und zwei Zahnräder als Zwischenzahnrad zwischen Motor und Rohr. Also habe ich passende Zahnräder aus Vollmessing gekauft, dazu noch paar Kugellager und eine Welle. Diese Zahnräder liegen natürlich in einer anderen Preisliga als Kunststoffzahnräder in Miniaturgröße, aber ich denke dass durch die Größe eine gewisse Robustheit mit einhergeht und das System dadurch lange in Betrieb stehen kann.
Kompliziert war noch ein passendes Zahnrad für das Rohr zu finden. Mein erster Gedanke war ein Zahnrad zu suchen, dessen Bohrung dem Außendurchmesser des Rohrs entspricht. Diese Suche ist aber erfolglos verlaufen. Dann bin ich auf Zahnräder mit Nabe gestoßen. Auch hier hatte zwar kein Zahnrad eine Nabe, deren Außendurchmesser dem Innendurchmesser des Rohrs entsprach, aber es gab eine Nabe, die nur ein Millimeter kleiner im Durchmesser war. Die 0,5 mm Luftspalt zwischen Rohrinnenwand und Nabe habe ich mit einer 0,5 mm starken Kunststoffplatte ausgefüllt und das Ritzel unter Zuführung von Sekundenkleber in das Rohr gepresst.
Aber was nützt einem nun die schönste Getriebekonstruktion wenn man die Zahnräder nicht lagern kann? Solch eine Lagerung mit konventioneller Säge und Bohrer selber bauen ist eigentlich nicht möglich. Zum einen haben die Kugellager solch spezielle Abmessungen, dass es dafür wohl keinen Bohrer gibt. Dann erfordert es noch solch hohe Präzision, dass man eigentlich ohne Fräsen nicht auskommt. Wie gut also, wenn man da jemanden kennt, der eine schöne Fräse daheim stehen hat. Ich habe mit unserem Bruchflieger Daniel Kontakt aufgenommen und er hat mir eine Lagerung aus Holz gefräst. Vorab musste ich dazu AutoCAD anwerfen und eine Zeichnung erstellen. Daniel hatte noch gute Ideen und baute gleich Abstandshalter ein, so dass der Getriebekasten am Ende nicht nur funktional und höchst präzise, sondern wie ich finde auch in einer gewissen Schönheit bei mir ankam. An dieser Stelle nochmal vielen Dank an Daniel für seine super gute Unterstützung und die schnelle Umsetzung.
Auf der unteren Platte werden die beiden Zwischenzahnräder eingesetzt. Das mittlere Kugellager ist für die Motorwelle.

Auf der oberen Platte folgen die beiden Rohre.

Dann kann beides verheiratet werden. In die Aussparung kommt der Getriebemotor hinein.


Ich habe mich hierzu für einen Getriebemotor von Conrad entschieden.

Das Zahnrad auf der Motorwelle fest zu montieren war gar nicht so einfach, aber ich habe es mit etwas Lötzinn dann geschafft.

Der Motor wird über einen Winkel und ein Holzbrett mit zwei Gewindeschrauben befestigt.


Fertig schaut die abenteuerliche Mechanik so aus:

Auch oben befindet sich eine Lagerung der beiden Rohre.

Hier sieht man einen beladenen und einen nicht beladenen Silo zu Testzwecken.

Und hier ein Video welches zeigt, dass alles funktioniert.
Leider dreht der Getriebemotor doch zu schnell, so dass bei normaler Betriebsspannung zu viel Schüttgut auf einmal in den Wagen fällt. Der Wagen belädt sich dann zu schnell, so dass es leicht passieren kann, dass er überfüllt wird. Hier muss ich also nochmal einen anderen Motor mit niedrigerer Umdrehungszahl kaufen.
Was derzeit noch ein kleines Problem ist, ist der „Nachlauf“ des Schüttguts. Bereits bei leichten Vibrationen fällt Schüttgut nach. Wenn kein Wagen auf dem Gleis steht, wird also im Laufe der Betriebstage das Gleis „befüllt“. Hier muss ich wohl noch etwas grübeln. Da ich aber ohnehin eine Steuerung für die Leuchtmelder zur Anzeige des Füllstands einbauen möchte, kann ich auch eine Automatik programmieren, die den Kolben bei längerer Nichtbenutzung wieder ein wenig nach unten fährt.
Nebenbei geht es auch an der Ausgestaltung weiter. Das Hauptgebäude neben den Silos wird wie der Silo auch mit Schrauben auf der Anlagenplatte befestigt. Hierzu wurden L-Profile an die Unterseite des Gebäudes geklebt. Die L-Profile haben mehr Verbindungsfläche zum Gebäude als die dünne Gebäudewand zum Boden.

Auf der Anlagenplatte werden Unterlegstücke eingebaut, welche den Höhenunterschied des Kopfsteinpflasters überbrücken. Außerdem noch ein Rohr. Wou denn das?

Von unten kommt ein Boden hinzu.


Von außen unscheinbar…

… Dach ab. Ich konnte es mir nicht verkneifen


Im Landschaftsbau geht es auf dem ersten Segment schon gut voran. Die Anhöhe am Seitenrand wird mit Styrodor und etwas Gips gestaltet.
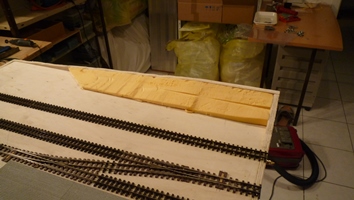
Mittlerweile ist dieses Segment bereits komplett geerdet und geschottert.

Als Gleisabschluss habe ich mich diesmal für Veit Prellböcke entschieden.

Und so schaut der Komplex aktuell aus.

Gruß
Dominik